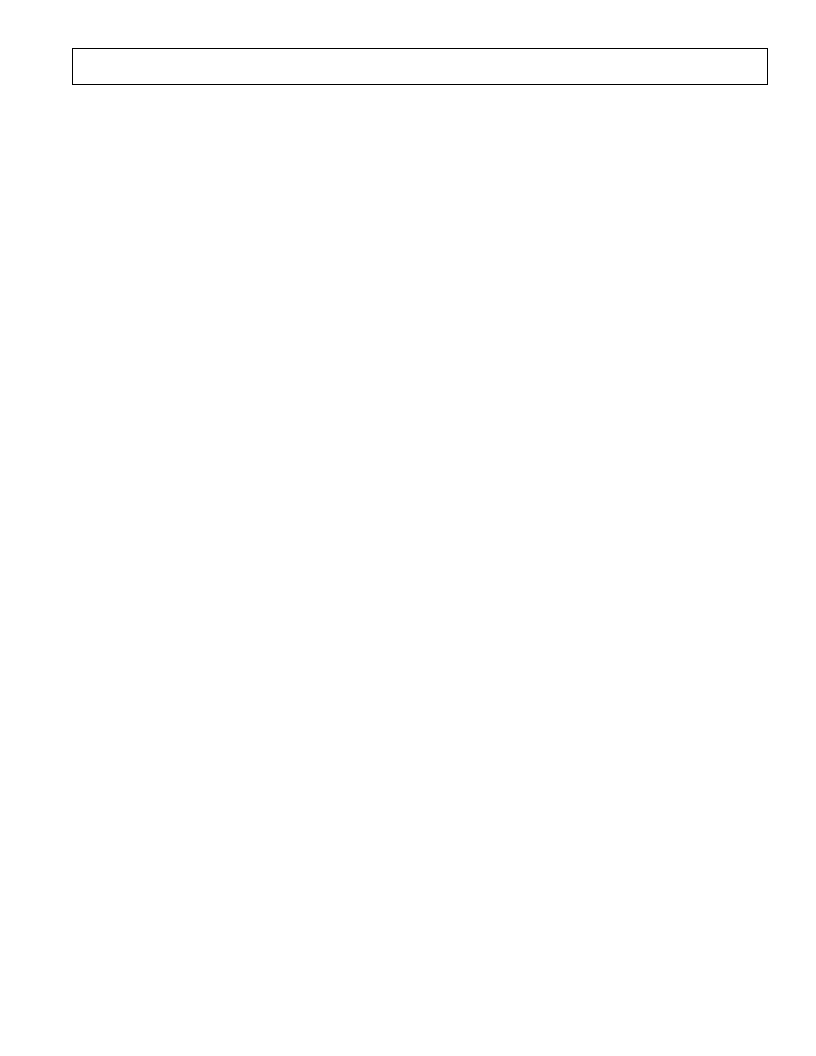
AD8150
–21–
REV. 0
external pin of the AD8150 projects into the package, and has a
bond wire connected to the chip inside. On-chip wiring then
connects to the collectors of the output transistors and to ESD
protection diodes.
Unlike some other high-speed digital components, the AD8150
does not have on-chip terminations. While this location would
be closer to the actual end of the transmission line for some
architectures, this concept can limit system design options. In
particular, it is not possible to bus more than two inputs or
outputs on the same transmission line and it is also not possible
to change the value of these terminations to use for different
impedance transmission lines. The AD8150, with the added
ability to disable its outputs, is much more versatile in these
types of architectures.
If the external traces are kept to a bare minimum, then the out-
put will present a mostly lumped capacitive load of about 2 pF.
A single stub of 2 pF will not seriously adversely affect signal in-
tegrity for most transmission lines, but the more of these stubs,
the more adverse their influence will be.
One way to mitigate this effect is to locally reduce the capacitance
of the main transmission line near the point of stub intersection.
Some practical means for doing this are to narrow the PC board
traces in the region of the stub and/or to remove some of the
ground plane(s) near this intersection. The effect of these tech-
niques will locally lower the capacitance of the main transmission
line at these points, while the added capacitance of the AD8150
outputs will
“
compensate
”
for this reduction in capacitance.
The overall intent is to create as uniform a transmission line as
possible.
In selecting the location of the termination resistors it is impor-
tant to keep in mind that, as their name implies, they should be
placed at either end of the line. There should be no or minimal
projection of the transmission line beyond the point where the
termination resistors connect to it.
EVALUATION BOARD
An evaluation board has been designed and is available to rapidly
test the main features of the AD8150. This board lets the user
analyze the analog performance of the AD8150 channels and
easily control the con
fi
guration of the board by a standard PC.
Differential inputs and outputs provide the interface for all chan-
nels with the connections made by a 50
, SMB-type connector.
This type of connector was chosen for its rapid mating and
unmating action. The use of SMB-type connectors minimizes
the size and minimizes the effort of rearranging interconnects
that would be required by using connectors such as SMA-type.
Configuration Programming
The board is con
fi
gurable by one of two methods. For ease of
use, custom software is provided that controls the AD8150
programming via the parallel port of a PC. This requires a user-
supplied standard printer cable that has a DB-25 connector at
one end (parallel- or printer-port interface) and a Centronix-
type connector at the other that connects to P2 of the AD8150
evaluation board. The programming with this scheme is done in
a serial fashion, so it is not the fastest way to con
fi
gure the AD8150
matrix. However, the user interface makes it very convenient to
use this programming method.
If a high-speed programming interface is desired, the AD8150
address and data buses are directly available on P3. The source
of the program signals can be a piece of test equipment, like the
Tektronix HFS-9000 digital test generator, or some other user-
supplied hardware that generates programming signals.
When using the PC interface, the jumper at W1 should be in-
stalled and no connections should be made to P3. When using
the P3 interface, no jumper is installed at W1. There are loca-
tions for termination resistors for the address and data signals if
these are necessary.
Power Supplies
The AD8150 is designed to work with standard ECL logic levels.
This means that V
CC
is at ground and V
EE
is at a negative sup-
ply. The shells of the I/O SMB connectors are at V
CC
potential.
Thus, when operating in the standard ECL con
fi
guration, test
equipment can be directly connected to the board, as the test
equipment will have its connector
“
shells
”
at ground potential also.
Operating in PECL mode requires V
CC
to be at a positive volt-
age, while V
EE
is at ground. Since this would make the shells of
the I/O connectors at a positive voltage, it can cause problems
when directly connecting to test equipment. Some equipment,
such as battery operated oscilloscopes, can be
“
floated
”
from
ground, but care should be taken with line-powered equipment
such that a dangerous situation is not created. Refer to the manual
of the test equipment that is being used.
The voltage difference from V
CC
to V
EE
can range from 3 V to 5 V.
Power savings can be realized by operating at a lower voltage
without any compromise in performance.
A separate connection is provided for V
TT
, the termination po-
tential of the outputs. This can be at a voltage as high as V
CC
,
but power savings can be realized if V
TT
is at a voltage that is
somewhat lower. Please consult elsewhere in the data sheet for
the speci
fi
cation for the limits of the V
TT
supply.
As a practical matter, current on the evaluation board will flow
from the V
TT
supply, through the termination resistors and then
through the AD8150 from its outputs to the V
EE
supply. When
running in ECL mode, V
TT
will want to be at a negative supply.
Most power supplies will not allow their ground to connect to
V
CC
and then the negative supply to V
TT
. This will require them
to source current from their negative supply, which will not re-
turn to the ground terminal. Thus, V
TT
should be referenced to
V
EE
when running in ECL mode or a true bipolar supply should
be used.
The digital supply is provided to the AD8150 by the V
DD
and
V
SS
pins. V
SS
should always be at ground potential to make it com-
patible with standard CMOS or TTL logic. V
DD
can range from
3 V to 5 V and should be matched to the supply voltage of the
logic used to control the AD8150. However, since PCs use 5 V
logic on their parallel port, V
DD
should be at 5 V when using a
PC to program the AD8150.
Software Installation
The software to operate the AD8150 is provided on two 3.5"
floppy disks. The software is installed by inserting Disk 1 into
the floppy drive of a PC and running the
“
setup.exe
”
program.
This will routinely install the software and prompt the user when to
change to Disk 2. The setup program will also prompt the user
to select the directory location to store the program.