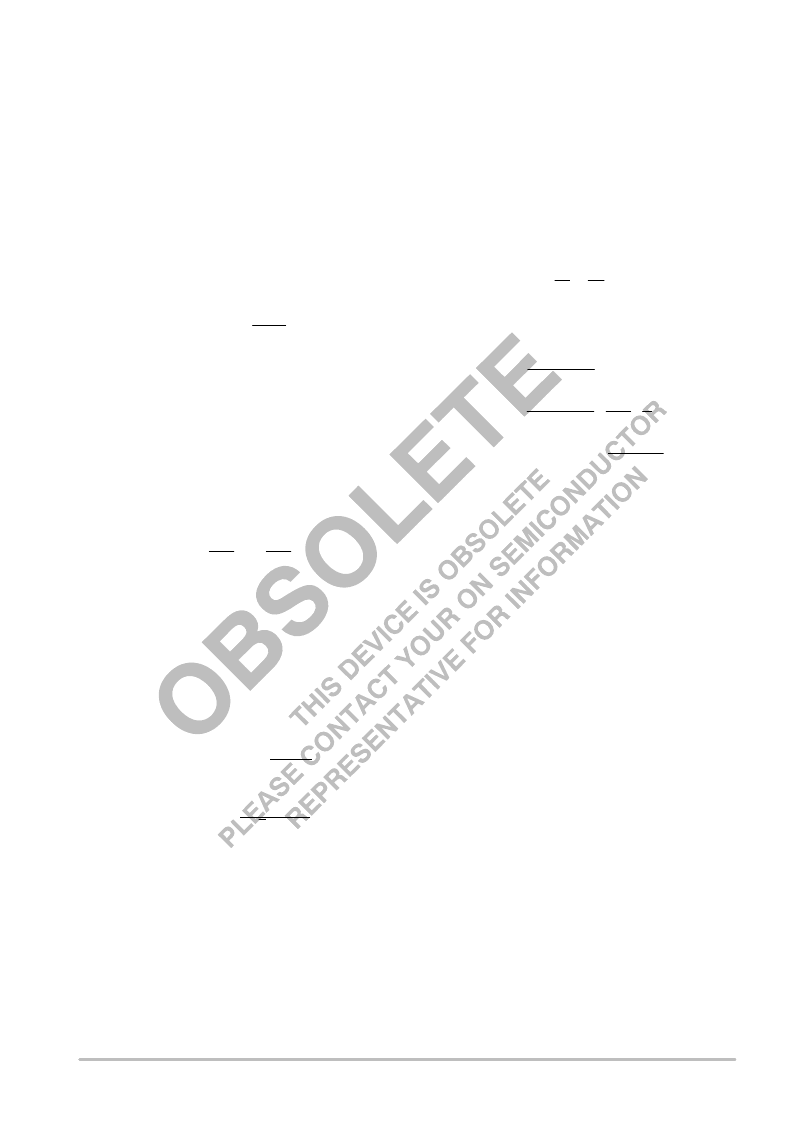
NCP1508
http://onsemi.com
12
APPLICATIONS INFORMATION
Component Selection
Input Capacitor Selection
In PWM operating mode, the input current is pulsating
with large switching noise. Using an input bypass capacitor
can reduce the peak current transients drawn from the input
supply source, thereby reducing switching noise
significantly. The capacitance needed for the input bypass
capacitor depends on the source impedance of the input
supply. The RMS capacitor current is calculated as:
IRMS
IO D
D
(eq. 1)
The maximum RMS current occurs at 50% duty cycle
with maximum output current, which is I
O,max
/2.
For NCP1508, a low profile ceramic capacitor of 10 F
should be used for most of the cases. For effective bypass
results, the input capacitor should be placed as close as
possible to the V
CC
Pin.
Inductor Value Selection
Selecting the proper inductor value is based on the
desired ripple current. The relationship between the
inductance and the inductor ripple current is given by the
equation in below.
Vout
Lfs
Large value inductors will have small ripple current and
low value inductor will have high ripple current. For
NCP1508, the compensation is internally fixed and a fixed
6.8 H inductor is needed for most of the applications.
iL
1
Vout
Vin
(eq. 2)
Output Capacitor Selection
Selecting the proper output capacitor is based on the
desired output ripple voltage. Ceramic capacitors with low
ESR values will have the lowest output ripple voltage and
are strongly recommended. The output ripple voltage is
given by:
Vc
iL
ESR
1
4fsCout
(eq. 3)
The RMS output capacitor current is given by:
IRMS(Cout)
VO
2 3
(1
D)
L
fs
(eq. 4)
Where f
s
is the switching frequency and ESR is the
effective series resistance of the output capacitor. A low
ESR, 22
F ceramic capacitor is recommended for
NCP1508 in most of applications. For example, with TDK
C2012X5R0J226 output capacitor, the output ripple is less
than 10 mV at 300 mA.
Design Example
As a design example, assume that the NCP1508 is used
in a single lithium
ion battery application. The input
voltage, V
in
, is 3.0 V to 4.2 V. Output condition is V
out
at
1.5 V with a typical load current of 120 mA and a maximum
of 300 mA. For NCP1508, the inductor has a predetermined
value, 6.8 H. The inductor ESR will factor into the overall
efficiency of the converter. The inductor needs to be
selected by the required peak current.
Equation 5 is the basic equation for an inductor and
describes the voltage across the inductor. The inductance
value determines the slope of the current of the inductor.
VL
L
Equation 5 is rearranged to solve for the change in
current for the on
time of the converter in Continuous
Conduction Mode.
(Vin
L
diL
dt
(eq. 5)
(eq. 6)
iL,pk
pk
Vout)
DTs
(Vin
Vout)
L
Vin
Vout
1
fs
iL,max
IO,max
iL,pk
pk
2
Utilizing Equations 6, the peak
to
peak inductor current
is calculated using the following worst
case conditions.
Vin,max
4.2 V,Vout
1.5 V,fs
1 MHz
20%,
L
6.8 H
10%,iL,pk
pk
Therefore, the inductor must have a maximum current
exceeding 405 mA.
Since the compensation is fixed internally in the IC, the
input and output capacitors as well as the inductor have a
predetermined value too: C
in
= 10 F and C
out
= 22 F. Low
ESR capacitors are needed for best performance.
Therefore, ceramic capacitors are recommended. Please
see Table 3 for recommended inductors and capacitors.
197 mA,iL,max
399 mA
PCB Layout Recommendations
Good PCB layout plays an important role in switching
mode power conversion. Careful PCB layout can help to
minimize ground bounce, EMI noise and unwanted
feedbacks that can affect the performance of the converter.
Hints suggested below can be used as a guideline in most
situations.
1. Use star
ground connection to connect the IC ground
nodes and capacitor GND nodes together at one point.
Keep them as close as possible. And then connect this to the
ground plane (if it is used) through several vias. This will
reduce noise in ground plane by preventing the switching
currents from flowing through the ground plane.
2. Place the power components (i.e., input capacitor,
inductor and output capacitor) as close together as possible
for best performance. All connecting traces must be short,
direct, and thick to reduce voltage errors caused by
resistive losses across these traces.
3. Separate the feedback path of the output voltage from
the power path. Keep this path close to the NCP1508
circuit. And also route it away from noisy components.