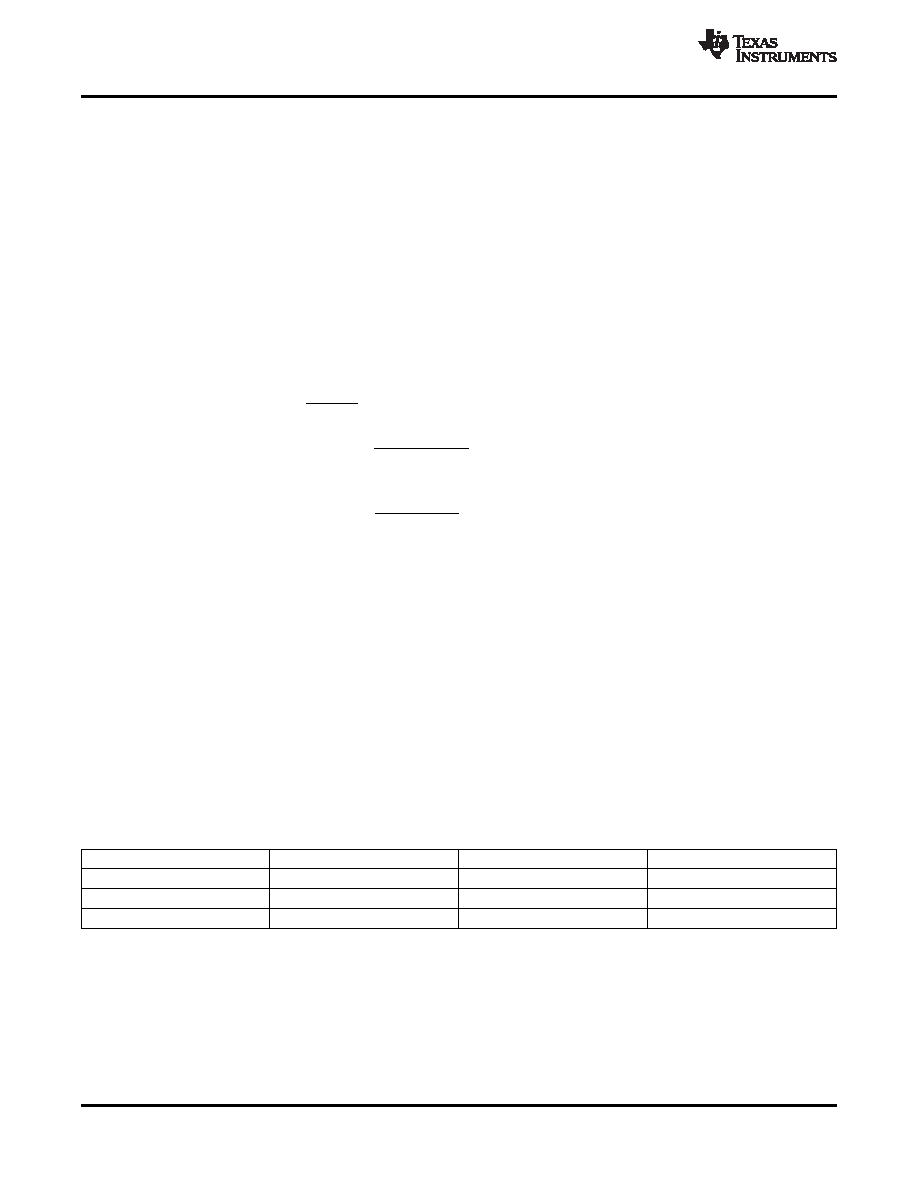
out
in
out
swpeak
in
swpeak
out
V
1. Converter Duty Cycle:
D =
V
(1
D)
2. Maximum output current: I
= I
D
2fs×L
V
(1 D)
3. Peak switch current:
I
= I
+
D
2fs
L
h
-
-
SLVSA22A – OCTOBER 2009 – REVISED JANUARY 2010
www.ti.com
Soft-Start (Buck Converter)
To avoid high inrush current during start-up, an internal soft-start is implemented. When the buck converter is
enabled, its current limit is reduced and it slowly rises (1ms to 2ms) to the switch current limit. For further inrush
current limitation, the switching frequency is reduced to 1/4 of the switching frequency fs until the feedback
voltage FB2 reaches 0.4V, then the switching frequency is set to 1/2 of fs until FB2 reaches 0.8V when the full
switching frequency fs (750kHz) is applied. See the internal Block diagram (Figure 26) for further explanation. The soft-start is typically completed in 1ms to 2ms.
Buck Converter Design Procedure
The first step in the design procedure is to verify whether the maximum possible output current of the buck
converter supports the specific application requirements. To simplify the calculation, the fastest approach is to
estimate the converter efficiency by taking the efficiency numbers from the provided efficiency curves or to use a
worst case assumption for the expected efficiency, e.g., 80%. The calculation must be for the maximum assumed
input voltage where the peak switch current is the highest. The inductor and external Schottky diode have to be
able to handle this current.
(15)
With;
Iswpeak = Converter peak switch current (minimum switch current limit = 1A)
fs = Converter switching frequency (typical 750kHz)
L = Selected inductor value
h = Estimated converter efficiency (use the number from the efficiency curves or 0.8 as an assumption)
Inductor Selection (Buck Converter)
The buck converter is able to operate with 6.8mH to 15mH inductors, a 10mH inductor is typical. The main
parameter for inductor selection is the saturation current of the inductor which should be higher than the
maximum output current plus the inductor ripple current as calculated in the Design Procedure section. The
highest inductor current occurs at maximum VIN. The alternative more conservative approach is to choose an
inductor with saturation current at least as high as the minimum switch current limit of 1A. Another important
parameter is the inductor dc resistance. Usually the lower the dc resistance the higher the efficiency; the type
and core material of the inductor influences the efficiency as well. The efficiency difference among inductors can
vary up to 10%. Possible inductors are shown in
Table 6.Table 6. Inductor Selection Buck Converter
INDUCTOR VALUE
COMPONENT SUPPLIER
SIZE (L×W×H mm)
Isat/DCR
10mH
Sumida CDRH3D23
3.9 × 3.9 × 2.5
0.85A/95m
10mH
Sumida CDRH3D28
4.0 × 4.0 × 3.0
1.1A/116m
10mH
Sumida CDRH4D22
5.0 × 5.0 × 2.4
0.8A/79m
Rectifier Diode Selection (Buck Converter)
To achieve high efficiency, a Schottky diode should be used. The reverse voltage rating should be higher than
the maximum output voltage of the buck converter. The average rectified forward current Iavg, the Schottky diode
needs to be rated for, is calculated as the off time of the buck converter times the output current.
Iavg = Iout × (1 – D)
(16)
24
Copyright 2009–2010, Texas Instruments Incorporated